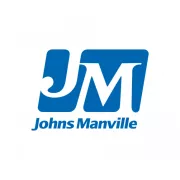
CNC Machinist - 2nd shift
Who We Are
Johns Manville is a leading manufacturer and marketer of premium-quality insulation and commercial roofing, along with glass fibers and nonwovens for commercial, industrial and residential applications. Our products are used in a wide variety of industries including building products, aerospace, automotive and transportation, filtration, commercial interiors, waterproofing and wind energy.
A proud member of the Berkshire Hathaway family of companies, we serve customers in more than 80 countries around the globe. We are committed to delivering positive and powerful experiences, because we are successful only when our employees and customers thrive. We are passionate, we care about people, we perform at a superior level, and we protect others and our environments.
Pay Range
$54,600.00-$75,100.00 AnnualThis is the base salary pay range that an applicant can expect to make upon hire. Pay within this range will vary based upon relevant experience, skills, and education among other factors. In addition, this position is eligible for an incentive bonus.
Position Overview: The CNC Machinist II is responsible for operating CNC machinery to produce precision parts and components. This role requires a strong focus on safety, quality, and efficiency. The CNC Machinist II will work under the supervision of senior machinists and supervisors to ensure that production goals are met while adhering to company policies and procedures.
2nd Shift Schedule: M-Th: 2:30pm-12:30am
Core Competencies:
Health, Safety and Environmental
- Selection and Use of PPE: Proper selection and use of plant PPE and task-specific PPE.
- Safety: Maintain safe work habits, recognize hazards, and ensure hand safety.
- Hazardous Communication: Understand and follow hazardous communication protocols and grinding safety.
- Control of Hazardous Energy (LOTO): Implement lockout/tagout procedures to control hazardous energy.
- Mobile and Powered Equipment Operation: Safely operate forklifts and powered pallet jacks.
- Crane Operations: Perform crane pre-use inspections, operation, and rigging.
- Machine Guarding: Ensure machine guarding and E-Stop awareness/operation.
- Policy Adherence: Follow JM Life Critical Policies.
- Waste Management: Manage waste streams including scrap metal and environmental considerations.
- JSA: Comprehend and sign off on Job Safety Analysis (JSA).
- Housekeeping: Maintain cleanliness and organization in the work area.
Computer/Data Entry
- Computer Skills: Basic computer skills including Microsoft O365 applications(Outlook, SharePoint, Excel, Word).
- Reporting Systems: Perform quality control inspections of parts on the machine and report any deficiencies via applicable quality reporting systems.
- Data Entry: Document work orders(via SAP ERP system) and other documentation required for quality control.
- SOPs: Locate and use Standard Operating Procedures (SOPs) via computer based library system (SharePoint).
- Training: Ability to navigate and utilize various computer based training (CBT) programs.
General Industry
- Tool Use: Use common hand and power tools effectively. Examples would be drills, grinders, deburring tools, surface grinder, etc.
- Measuring: Ability to use precision measuring tools such as tape measures, scales, micrometers, and calipers to perform dimensional tolerancing of parts.
- Shop Math: Apply basic shop math including measurements, geometry, volume, and area.
- Blueprint Interpretation: Interpret blueprints and understand entry-level GD&T.
Job/Trade Specific
- Machine Maintenance: Conduct basic machine maintenance and pre-use inspections.
- Material Handling: Handle and identify materials, including alloys.
- Calibration: Verify that measuring instruments such as gauges, calipers and micrometers are calibrated and are in good working order.
- Set-Up Notes: Apply set-up notes and make programming adjustments/updates.
- Tolerances: Hold required tolerances and perform visual inspections.
- Production Standards: Meet production standards and isolate causes of out-of-tolerance part features.
- Part Quality: Complete finishing and deburring on parts as necessary.
- CNC Operations: Perform expert-level CNC operations including start-up, safe operations, and shut down.
- Production Cell Operations: Operate in a production cell with multiple work centers.
- Speeds and Feeds: Have a advanced knowledge of speeds and feeds, tool touch-off, and setting offsets as they pertain to machining.
- Workpiece Handling: Load, feed, and unload workpieces.
- Tool Changes: Demonstrate ability to complete tool changes including changing jaws and cutting tools/holders.
- Fixturing: Ability to properly install and utilize task-specific fixturing.
- Code: Knowledge in G and M code as applies to CNC Machining
- Continuous Improvement: Help develop continuous improvement ideas and fixture design.
- Collaboration: Collaborate with engineering, quality and production teams to troubleshoot and resolve any machining and programming issues.
- Mentor: Mentor less experienced operators/machinists and contribute to their professional development.
Department Specific Requirements
- CNC
- CNC Lathe Operations: Ability to perform multiple set-ups daily and operate CNC lathe machines as detailed in work instructions and routings with little or no oversight. Typically expect at between 10,000-15,000 hours of CNC lathe operation.
- CNC Lathe Operations: Perform turning (straight/taper) using canned cycles.
- CNC Mill Operations: Ability to perform multiple set-ups daily and operate 5-axis CNC mill machines as detailed in work instructions and routings with little or no oversight. Typically expect at between 10,000-15,000 hours of CNC lathe operation.
- CNC Gundrill Operation: Ability to perform multiple set-ups daily and operate gundrill machines as detailed in work instructions and routings with little or no oversight.
- Programs: Ability to move programs via Predator to/from machines and server.
- Programs: Demonstrate ability to prove out complex programs on both CNC mill and Lathe.
- Troubleshooting: Troubleshoot malfunctions and demonstrate ability to isolate the cause of machine alarms
- Quality Inspections: Perform in-process inspection activities when necessary including first article inspections(FAI) as required.
- Code: Knowledge in G and M code as applies to CNC Machining and ability to program at the machine.
- Tooling: Advanced understanding of tooling with the ability to select proper tooling for both lathe and mill operations based on application.
- Tooling/Fixtures: Ability to collaborate with development fixturing and machine fixtures once designed.
- Setup: Perform Complex Set Ups to Complete Machining Requirements
- Proficiency: See CNC Department Skills Matrix for requirement minimum part and machine requirements.
- Alloy
- CNC Lathe Operations: Thorough knowledge of and be experienced in set-up and operation of CNC lathe machines with little or no oversight.
- Proficiency: See Alloy Department Skills Matrix for requirement minimum part requirements.
Minimal Qualifications:
- High school diploma or equivalent.
- Basic understanding of CNC machinery and operations.
- Ability to read and interpret blueprints and technical drawings.
- Strong attention to detail and commitment to quality.
- Good communication and teamwork skills.
- Willingness to learn and follow safety protocols.
- Minimum of 4- 6 years CNC operational experience or closely related trade.
Preferred Qualifications:
- Associate degree or certificate in CNC Machining or similar program from an accredited institution.
- In addition to the competencies mentioned above an ideal candidate would have 15+ years of CNC operation
- Proficient with live tooling and multiple axis machining.
- Proficient with intermediate CNC programming using Mastercam
Physical Requirements:
- Ability to lift and move materials up to 50 pounds.
- Standing for extended periods.
- Manual dexterity and hand-eye coordination.
Work Environment:
- Manufacturing plant with exposure to noise, dust, and machinery.
- Use of personal protective equipment (PPE) as required.
Please Keep in Mind
If you do not meet 100% of these requirements, we at JM still want to hear from you. So, if you are interested in the role, we encourage you to apply so we can learn how your skills and talents can contribute to our team.
Benefits
Johns Manville (JM) offers a wide range of benefits to employees. Some are subsidized by the company and others are fully employee-paid. Health benefits include a choice of comprehensive medical plans, a dental plan, vision plan, wellness program and critical illness insurance. JM sponsors a 401(k) plan which includes a sizeable company match. JM offers paid vacation and also provides paid sick and parental leave for eligible employees.
Additionally, Johns Manville provides basic life Insurance, short-term and long-term disability coverage, an employee assistance program, and business travel accident coverage. Supplemental life insurance and accidental death and dismemberment insurance are available as well. The company also offers a variety of tax saving accounts; health spending account, traditional flexible spending account, and a dependent care spending account. JM also offers a tuition reimbursement program for undergraduate and certain graduate programs.
Johns Manville supports employee growth with vast educational opportunities and a company-wide mentoring program. This program pairs employees and leaders to grow skills, build stronger internal networks and strengthen the company’s succession planning process. Johns Manville also offers soft and hard skills training facilitated by internal and external presenters. Our talent management team prioritizes the holistic growth of our workforce.
Diversity & Inclusion
Johns Manville believes diversity and inclusion in our workplace is critical for the long-term success of our company. We are committed to retaining, developing and attracting a diverse workforce that fosters an inclusive work environment in which all employees are treated with dignity and respect. This is the right thing to do for our employees, our company and our communities. Our D&I council is composed of employees from locations across North American & Europe who meet regularly and work to promote and foster an environment of inclusion. Born from our D&I council is our network of employee resource groups (ERGs) that are focused on supporting diverse communities in the workplace. Review more about our diversity & inclusion initiatives on JM’s Career page.
Incumbent must be physically able to perform essential job functions. Reasonable accommodations may be made to enable individuals with disabilities to perform essential job functions.
We are proud to be an Equal Opportunity/Affirmative Action employer. We maintain a drug-free workplace and perform pre-employment substance abuse testing.
Salary range
- $54,600 - $75,100